Spis treści
Co to jest gwint M10?
Gwint M10 to metryczny gwint o średnicy nominalnej 10 mm, który zdobył popularność w różnych dziedzinach inżynieryjnych i budowlanych. Charakteryzuje się skokiem wynoszącym 1,5 mm, co oznacza, że podczas jednego pełnego obrotu element przesuwa się o 1,5 mm wzdłuż osi. Jest to bardzo wszechstronny gwint, co czyni go idealnym do licznych zastosowań. Występuje w dwóch rodzajach:
- gwint zewnętrzny, wykorzystywany na śrubach,
- gwint wewnętrzny, obecny w gwintowanych otworach.
Jego wartość nominalna odpowiada średnicy zewnętrznej gwintu zewnętrznego – w przypadku M10 mówimy więc o 10 mm. Znajduje on szerokie zastosowanie w konstrukcjach metalowych, co związane jest z jego wytrzymałością oraz łatwością montażu, umożliwiając skuteczne łączenie różnych komponentów. Gwint M10 jest często wykorzystywany w branżach takich jak:
- motoryzacja,
- budownictwo,
- produkcja maszyn.
Aby uzyskać precyzyjne gwintowanie, warto zastosować wiertło o średnicy 8,5 mm. Przełoży się to na odpowiednie wymiary otworu, co zapewni mocne i stabilne połączenie. Kluczowe jest również odpowiednie dobieranie narzędzi do gwintowania oraz uwzględnienie tolerancji otworów, aby uniknąć trudności podczas montażu. Tak więc, gwint M10 odgrywa istotną rolę w wielu systemach łączeń śrubowych, mając ogromne znaczenie dla współczesnego przemysłu.
Jakie wymiary ma gwint M10?
Gwint M10 charakteryzuje się średnicą nominalną wynoszącą 10 mm, co znacznie ułatwia jego identyfikację. Standardowy skok dla tego gwintu zazwyczaj wynosi 1,5 mm, co odnosi się do odległości pomiędzy wierzchołkami kolejnych zwojów. Oprócz tego, dostępne są także gwinty drobnozwojne M10, które cechują się mniejszym skokiem, co sprawia, że nadają się doskonale do precyzyjnych zastosowań.
Warto również zwrócić uwagę na średnicę rdzenia gwintu M10, która zawsze jest mniejsza od 10 mm. W przypadku gwintu metrycznego M10 średnica rdzenia oscyluje około 8,4 mm. Jest to istotna informacja, gdyż ma kluczowe znaczenie dla zapewnienia odpowiedniej nośności połączeń gwintowych w różnych zastosowaniach.
Wielorakie zastosowanie gwintu M10 w branżach takich jak motoryzacja czy budownictwo świadczy o jego uniwersalności. Znajomość wymiarów gwintu jest niezwykle istotna, ponieważ pozwala na zapewnienie solidnych połączeń w konstrukcjach metalowych oraz dobór właściwych narzędzi do obróbki, takich jak wiertła czy gwintowniki.
Jakie skoki mają gwinty M10?
Gwinty M10 różnią się między sobą skokami, co ma istotny wpływ na ich zastosowanie. Standardowe skoki wynoszą 1,5 mm, co oznacza, że przy każdym obrocie śruby przesuwa się ona o tę wartość. Istnieją również gwinty drobnozwojne M10, które charakteryzują się mniejszymi skokami, na przykład:
- 1,25 mm,
- 1 mm.
Takie drobnozwojne wersje są doskonałe do precyzyjnych zastosowań, ponieważ umożliwiają lepsze dopasowanie do nacięć śrubowych. Wybór odpowiedniego skoku powinien być ściśle uzależniony od specyfiki użytkowania, gdyż ma to znaczący wpływ na funkcjonalność oraz trwałość połączenia. W branżach takich jak motoryzacja i budownictwo, gdzie istotna jest wysoka nośność i stabilność, staranny dobór skoku staje się kluczowy dla efektywności całej konstrukcji. Odpowiednio dobrany gwint M10 nie tylko zapewnia odpowiednie właściwości mechaniczne, ale także znacząco zwiększa żywotność połączonych elementów.
Jakie są różnice między gwintem M10 a innymi gwintami, jak M8 czy M5?
Gwinty M10, M8 i M5 różnią się przede wszystkim średnicą oraz skokiem. Dla przypomnienia:
- gwint M10 ma średnicę 10 mm,
- gwint M8 to 8 mm,
- gwint M5 – 5 mm.
Ta różnorodność wpływa na wytrzymałość połączeń śrubowych oraz siły dokręcania, gdzie większa średnica zazwyczaj oznacza mocniejsze połączenie, co jest kluczowe w konstrukcjach wymagających dużej nośności. Standardowy skok gwintu:
- M10 wynosi 1,5 mm, co umożliwia efektywne i stabilne mocowanie,
- M8 skok wynosi najczęściej 1,25 mm,
- M5 to 0,8 mm, co sprawia, że mniejsze skoki przekładają się na wyższą precyzję.
W związku z tym, gwinty M8 oraz M5 sprawdzają się lepiej w zastosowaniach, gdzie dokładność jest priorytetem. Różnice te mają istotne znaczenie w kontekście ich zastosowań. Gwint M10 jest często używany w elementach narażonych na większe obciążenia, takich jak w motoryzacji czy budownictwie, natomiast M8 i M5 zyskują na popularności w lżejszych konstrukcjach. Ostatecznie, wybór odpowiedniego gwintu powinien być dostosowany do specyfikacji technicznych projektu, dlatego zrozumienie tych różnic jest kluczowe dla inżynierów oraz techników.
Jakie inne gwinty są zbliżone do gwintu M10?
Kiedy mówimy o gwincie M10, warto zauważyć, że w podobnych rozmiarach znajdują się gwinty:
- M8, który ma średnicę 8 mm i standardowy skok wynoszący 1,25 mm,
- M12, o średnicy 12 mm, przewyższający M10, co przekłada się na jego większą wytrzymałość i szersze możliwości zastosowań.
Warto również rozważyć gwinty calowe, na przykład 3/8 cala (około 9,525 mm średnicy), jako opcje zamienne dla M10. Należy pamiętać, że różnice w skoku i średnicy stawiają nas przed koniecznością precyzyjnego dopasowania do specyficznych potrzeb inżynieryjnych. Wybierając odpowiedni gwint, warto mieć na uwadze nie tylko charakter projektu, ale również wymagania dotyczące nośności i precyzji wykonania.
W jakich konstrukcjach metalowych wykorzystuje się gwint M10?
Gwint M10 zyskał szerokie zastosowanie w różnych konstrukcjach metalowych. Dzięki swojej elastyczności oraz odpowiedniej wytrzymałości, doskonale sprawdza się tam, gdzie niezbędne są stabilne połączenia śrubowe. Stosuje się go na przykład w:
- budowie pojazdów,
- montażu maszyn,
- meblarstwie metalowym.
Gwint M10 często występuje w elementach ram i stelaży, co czyni go niezwykle przydatnym w wielu dziedzinach. Posiadając doskonałe właściwości mechaniczne, staje się niezastąpiony w połączeniach, które muszą wytrzymać średnie obciążenia. Co więcej, gwinty M10 efektywnie łączą różnorodne materiały, co jest istotne w branży przemysłowej i budowlanej. Istotnym aspektem jest również to, że wybór właściwego gwintu oraz jego umiejscowienie w konstrukcji znacząco wpływają na bezpieczeństwo oraz trwałość całego systemu. Standardowe wymiary tego gwintu ułatwiają zarówno montaż, jak i konserwację konstrukcji, co czyni go kluczowym elementem w nowoczesnym budownictwie i inżynierii.
Jakie wymiary otworu są kluczowe dla gwintu M10?
Średnica otworu przygotowanego pod gwint M10, wynosząca 8,5 mm, jest kluczowym wymiarem zapewniającym prawidłowe nacięcie gwintu. Taki wymiar wpływa na wytrzymałość i jakość połączeń, co ma istotne znaczenie w wielu zastosowaniach.
Również tolerancja otworu jest istotna, gdyż musi odpowiadać klasie dokładności gwintu. Jeśli średnica otworu jest zbyt mała, może to prowadzić do uszkodzenia, natomiast zbyt luźny otwór osłabia całą konstrukcję. Zazwyczaj tolerancje dla otworów na gwint M10 powinny być w przedziale H7, co pozwala na uzyskanie dokładnych i stabilnych połączeń.
Dla inżynierów oraz techników zajmujących się obróbką metalu kluczowe jest rozumienie wymagań dotyczących średnicy otworu. Odpowiedni dobór tych wymiarów przekłada się nie tylko na jakość gwintowania, ale również zwiększa efektywność wykorzystania gwintu M10 w różnorodnych konstrukcjach metalowych.
Jakie wiertło wybrać pod gwint M10?
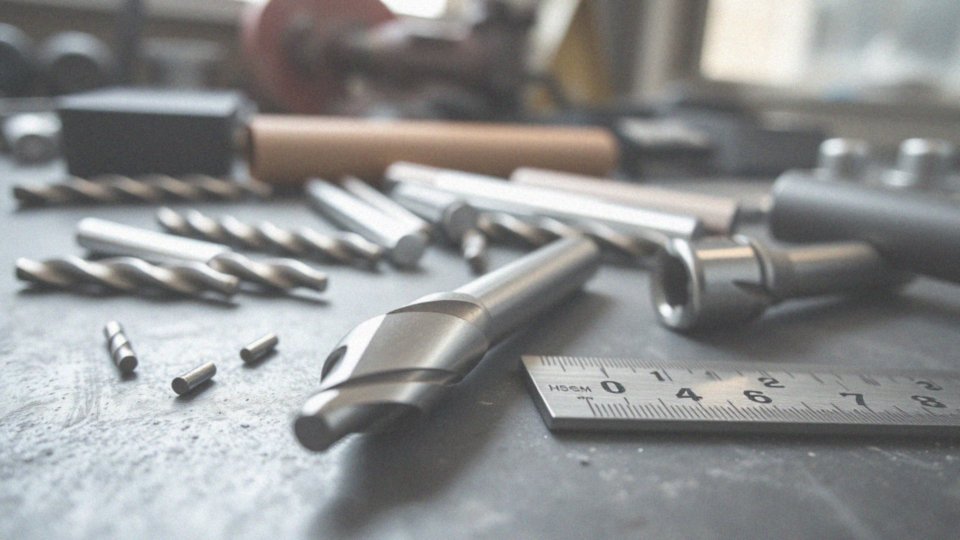
Aby utworzyć otwór pod gwint M10, niezbędne jest użycie wiertła o średnicy 8,5 mm. Wybór właściwego narzędzia jest niezwykle istotny, gdyż wpływa na dokładność wiercenia oraz jakość powstałego gwintu.
Wiertła wykonane z:
- metalu HSS,
- metalu kobaltowego,
są jednymi z najlepszych opcji dostępnych na rynku. Ich cechą szczególną jest duża odporność na wysokie temperatury oraz uszkodzenia mechaniczne, co gwarantuje długi okres eksploatacji. Kąt wierzchołkowy wiertła również odgrywa kluczową rolę. W przypadku miękkich metali, takich jak aluminium, idealnym wyborem będzie kąt 118 stopni. Natomiast dla stalowych materiałów lepiej zastosować kąt 135 stopni.
Odpowiednie dobieranie kątów wiertła pozwala na uzyskanie gładkich otworów, co jest niezbędne do zapewnienia mocnych połączeń. Właściwie dobrane wiertło nie tylko przyspiesza proces gwintowania, ale także minimalizuje ryzyko uszkodzeń narzędzi oraz elementów, które obrabiamy. Zapewnienie wysokiej jakości wierteł do gwintu M10 znacząco wpływa na efektywność oraz trwałość zamontowanych komponentów.
Jakie są wymagania dotyczące średnicy wiertła do gwintu M10?
Średnica wiertła do gwintu M10 wynosi 8,5 mm, co stanowi optymalny rozmiar do uzyskania odpowiedniego otworu. Warto jednak pamiętać, że te wartości mogą się różnić w zależności od tolerancji oraz rodzaju używanego materiału, więc przy wyborze odpowiedniego wiertła należy wziąć pod uwagę te aspekty. Powinien on być mniejszy od nominalnej średnicy gwintu, która wynosi 10 mm. Dzięki temu zachowujemy materiał, który jest niezbędny do nacięcia gwintu.
Właściwy dobór średnicy wiertła ma kluczowe znaczenie dla jakości gwintowania. Do najważniejszych aspektów należy:
- zbyt mały rozmiar może utrudnić proces nawiercania,
- zbyt duży rozmiar może osłabić połączenie,
- negatywny wpływ na wytrzymałość całej konstrukcji.
Dlatego zachowanie odpowiednich tolerancji jest niezwykle istotne. W przypadku gwintu M10 zaleca się tolerancje w klasie H7. Tak precyzyjny wybór wiertła o średnicy 8,5 mm ma ogromne znaczenie w inżynierii oraz budownictwie, gdzie stabilność połączeń jest kluczowa.
Jakie cechy powinno mieć wiertło do gwintu M10?
Wiertło do gwintu M10 powinno posiadać kilka kluczowych właściwości, które znacząco wpływają na jego efektywność:
- materiał wykonania powinien charakteryzować się wyjątkową trwałością,
- wiertła z wysokiej jakości stali szybkotnącej (HSS) lub kobaltowe cieszą się najlepszą opinią,
- kąt wiertła – dla materiałów miękkich, takich jak aluminium, powinien wynosić 118 stopni,
- dla stali warto postawić na kąt 135 stopni,
- geometria rowków wiórowych – dobrze zaprojektowane rowki skutecznie usuwają wióry,
- wiertła z węglików spiekanych mogą znacząco wydłużyć żywotność narzędzia,
- wysoka precyzja wykonania oraz ostry wierzchołek wiertła mają kluczowe znaczenie dla dokładności i jakości gwintowania.
Wybór odpowiedniego wiertła, które spełnia te wszystkie kryteria, jest niezbędny do uzyskania trwałych i stabilnych połączeń gwintowych.
Na co zwrócić uwagę przy doborze wiertła pod gwint M10?
Wybór odpowiedniego wiertła do gwintu M10 wymaga uwzględnienia kilku kluczowych aspektów. Przede wszystkim materiał, w którym zamierzamy wiercić, odgrywa znaczną rolę. Na przykład, w przypadku obróbki metalu, warto zdecydować się na wiertła:
- HSS,
- kobaltowe,
- wykonane z węglika spiekanego.
Charakteryzują się one wysoką odpornością i trwałością. Istotnym elementem jest również średnica wiertła, która dla gwintu M10 powinna wynosić 8,5 mm. Pamiętaj, aby wiertło było ostre oraz w dobrym stanie – ma to bezpośredni wpływ na jakość wykonywanego gwintu oraz efektywność wiercenia.
Kąt wierzchołkowy wiertła również powinien być dopasowany do rodzaju obrabianego materiału. Na przykład:
- dla miękkich metali takich jak aluminium, idealny będzie kąt 118 stopni,
- natomiast w przypadku stali lepszym rozwiązaniem okaże się kąt 135 stopni.
Użycie chłodziwa podczas wiercenia to dodatkowy atut, który wspomaga proces oraz redukuje ryzyko uszkodzeń zarówno wiertła, jak i obrabianego materiału. Nie można również pominąć klas tolerancji otworów – mają one kluczowe znaczenie dla precyzji gwintowania oraz jakości połączeń gwintowych.
Jak dobór wiertła wpływa na proces gwintowania?
Wybór odpowiedniego wiertła ma ogromne znaczenie w procesie gwintowania. Jeśli średnica wiertła nie jest właściwie dobrana, mogą wystąpić poważne trudności. Na przykład, aby utworzyć gwint M10, należy zastosować otwór o średnicy 8,5 mm. Taki rozmiar sprzyja łatwemu nacięciu gwintu oraz podnosi trwałość całego połączenia. Zbyt małe wiertło może znacznie utrudnić wykonanie gwintu, a zbyt duże osłabi jego wytrzymałość.
Warto także zwrócić uwagę na materiał, w którym wykonujemy otwór. Wiertła wykonane z wysokiej jakości stopów metalowych, takich jak HSS czy kobaltowe, charakteryzują się dużą odpornością na wysokie temperatury oraz uszkodzenia mechaniczne, co przekłada się na ich dłuższą żywotność. Kąt wiertła, dostosowany do obrabianego materiału, ma istotny wpływ na jakość otworu. Na przykład, kąt 135 stopni sprawdza się doskonale w pracy ze stalą, co pozwala uzyskać gładki i mocny gwint.
Nie mniej ważna jest także geometria rowków wiórowych w wiertle, która ułatwia skuteczne usuwanie wiórów. To kluczowy element dbałości o jakość gwintu. Podejmując decyzję o wyborze wiertła, pamiętajmy również o klasach tolerancji otworów, co zapewnia idealne dopasowanie do gwintownika. Odpowiedni dobór wiertła dla gwintu M10 to zatem podstawa, która zapewnia wysoką efektywność, trwałość oraz stabilność połączeń w różnorodnych konstrukcjach metalowych.
Jakie wiertła są odpowiednie dla różnych typów gwintów?
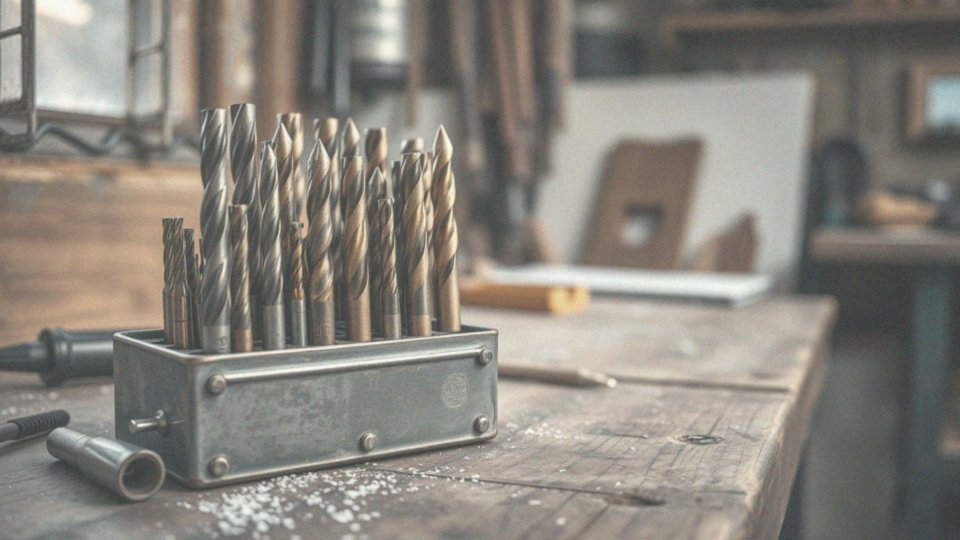
Właściwy dobór wierteł dostosowanych do różnych typów gwintów ma kluczowe znaczenie dla osiągnięcia zadowalających efektów podczas gwintowania. Na przykład, wybierając gwinty metryczne, takie jak M10, zaleca się użycie wiertła o średnicy 8,5 mm, co pozwala na odpowiednie przygotowanie otworu.
W przypadku gwintów drobnozwojnych, należałoby sięgać po wiertła o nieco większej średnicy niż nominalna, co korzystnie wpływa na jakość nacięcia. Natomiast dla gwintów rurowo-walcowych i stożkowych warto używać specjalistycznych narzędzi, które idealnie pasują do ich specyfikacji.
Wiertła do gwintów rurowo-walcowych mają unikalny kształt wierzchołka, co znacznie ułatwia wiercenie w materiałach rurkowych. Nie bez znaczenia jest także materiał, z którego wykonano wiertło.
- w przypadku metalu, najlepsze efekty osiąga się przy użyciu narzędzi z metalu HSS lub kobaltowego,
- które cechują się wysoką odpornością na temperaturę,
- kąt wiertła ma również wpływ na jakość nawiercania,
- dla stalowych komponentów najbardziej efektywny jest kąt 135 stopni,
- który sprzyja uzyskaniu gładkiego otworu.
Taki detal z kolei poprawia przyczepność gwintu. Staranny wybór wiertła i zwrócenie uwagi na szczegóły przekładają się na precyzyjne i trwałe połączenia gwintowe, co jest niezwykle istotne w inżynierii oraz budownictwie. Świadome podejście do wyboru narzędzi i metod gwintowania nie tylko zwiększa efektywność, ale także wytrzymałość całych konstrukcji.
Jakie materiały są najlepsze dla wierteł do metalu?
Wybór odpowiednich materiałów do produkcji wierteł metalowych ma kluczowe znaczenie dla skuteczności wiercenia oraz trwałości gwintów. W czołówce najczęściej wybieranych surowców znajdują się:
- stal szybkotnąca (HSS),
- stal szybkotnąca wzbogacona kobaltem (HSS-Co),
- węgliki spiekane.
Wiertła HSS charakteryzują się odpornością na wysokie temperatury oraz uszkodzenia, co czyni je idealnymi do obróbki stali, aluminium i innych miękkich metali. Z kolei wiertła HSS-Co oferują jeszcze wyższą trwałość, dlatego szczególnie polecane są do stosowania w bardziej wymagających materiałach, takich jak stal nierdzewna. Wiertła z węglików spiekanych są absolutnym liderem pod względem wytrzymałości i doskonale sprawdzają się w wierceniu w bardzo twardych materiałach.
Podczas zakupu wiertła istotne jest również zwrócenie uwagi na jego kąt. Musi on być dopasowany do rodzaju metalu, który zamierzamy obrabiać. Kąt 135 stopni jest szczególnie efektywny w przypadku wiercenia w stali, co znacząco wpływa na jakość uzyskanego otworu. Odpowiedni dobór materiałów oraz parametrów wiertła ma zatem ogromny wpływ na efektywność i żywotność narzędzi używanych podczas procesu gwintowania.
Jakie są zasady tolerancji otworów przy gwintowaniu M10?
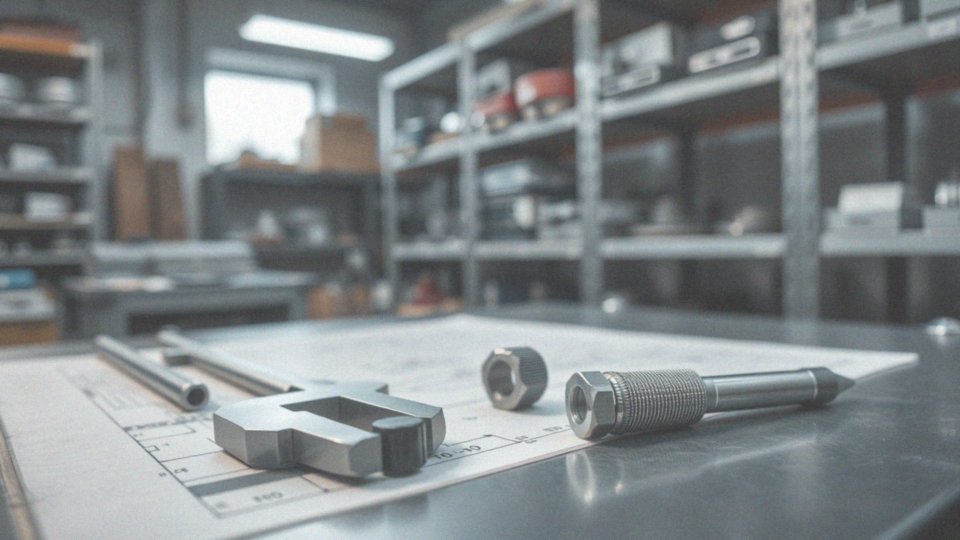
Tolerancja otworu przy gwintowaniu M10 odgrywa kluczową rolę w uzyskiwaniu precyzyjnych i stabilnych połączeń. W przypadku gwintów metrycznych powszechnie stosuje się wartości tolerancji H7 lub H8. Oznacza to, że dopuszczalne odchylenia średnicy otworu, który ma nominalną wartość 8,5 mm, muszą być starannie monitorowane.
Tolerancja | Maksymalna średnica (mm) | Minimalna średnica (mm) |
---|---|---|
H7 | 8,55 | 8,45 |
H8 | 8,6 | 8,4 |
Wyższa klasa dokładności gwintu zazwyczaj przekłada się na mniejszą tolerancję otworu. Co więcej, w branżach takich jak motoryzacja i lotnictwo, wymagania odnośnie tolerancji są jeszcze bardziej precyzyjne. Zbyt luźny otwór może osłabić stabilność połączenia, natomiast zbyt ciasny może prowadzić do uszkodzeń gwintu podczas montażu. Dlatego dbanie o odpowiednie tolerancje jest niezwykle istotne, by zapewnić długotrwałą i bezproblemową pracę konstrukcji metalowych z wykorzystaniem gwintu M10. Takie starania przynoszą nie tylko wytrzymałość, ale również gwarantują bezpieczeństwo w realizowanych projektach.
Jakie narzędzia, takie jak gwintownik i narzynka M10, są potrzebne do gwintowania?
Aby skutecznie wykonać gwint M10, niezbędne są specjalistyczne narzędzia, które gwarantują wysoką jakość nacięcia oraz trwałość połączeń. Najważniejszym z nich jest gwintownik M10, który służy do tworzenia gwintu wewnętrznego. Jego użycie pozwala uzyskać precyzyjny kształt gwintu, co przekłada się na stabilność oraz wytrzymałość całej konstrukcji. Równie istotna jest narzynka M10, która służy do gwintowania zewnętrznego; jej rola w tym procesie również jest kluczowa.
Narzędzia powinny być zamocowane w odpowiednich uchwytach, aby zapewnić pełną kontrolę i dokładność podczas całego gwintowania. Konieczne jest również zastosowanie wiertła o średnicy 8,5 mm, które przygotowuje otwór do gwintu; jego jakość ma istotny wpływ na końcowy efekt.
Dodatkowo, wykorzystanie chłodziwa w trakcie pracy znacząco wspomaga proces gwintowania, gdyż zmniejsza tarcie i przedłuża żywotność narzędzi. Odpowiednie warunki obróbcze są niezbędne do uzyskania optymalnych rezultatów. Bez stosownego wyposażenia, proces gwintowania M10 może być znacznie mniej efektywny, co ma kluczowe znaczenie w licznych zastosowaniach inżynieryjnych oraz budowlanych.